Research Team Utilizes Dual Catalysts for Enhanced Safety and Environmental Friendliness in Common Chemical Production
Reforming the chemical industry’s environmental reputation has been a longstanding challenge, plagued by images of smokestack emissions and hazardous waste discharge. Caltech’s Karthish Manthiram, a professor of chemical engineering and chemistry, and a William H. Hurt Scholar, is dedicated to advancing eco-friendly chemistry.
In a Science journal publication, Manthiram’s lab unveils a catalyst designed for the production of a commonly used chemical feedstock, propylene oxide, without resorting to the conventional use of toxic chemicals. Propylene oxide serves various purposes, including the manufacturing of foams, plastics, antifreeze, and applications in disinfection and sterilization.
Traditionally, its production involves reacting propylene with either hypochlorous acid or hydrogen peroxide, each presenting its own set of environmental and safety concerns. “Hypochlorous acid produces a chloride byproduct, which is discharged into the environment, leading to limited permits for hypochlorous acid processes. The shift to peroxide-based processes has safety challenges, as the presence of hydrogen peroxide in contact with organic compounds poses an explosion risk,” explains Manthiram.
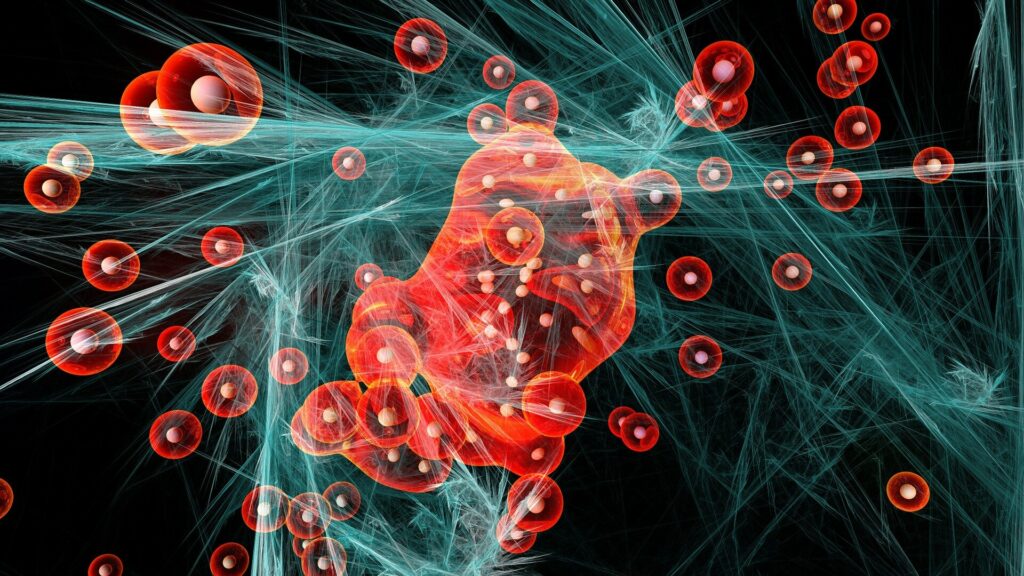
The objective of the group was to devise a secure approach to propylene epoxide production that avoids environmental discharge and minimizes the carbon footprint. The team initially sought a catalyst capable of utilizing the oxygen atom in a water molecule to produce propylene epoxide, with hydrogen gas being the only byproduct—useful as fuel or for manufacturing other chemicals.
The team identified two catalysts, platinum oxide and palladium oxide, each individually performing the desired reaction but with limitations. Platinum oxide produced propylene epoxide efficiently but generated many undesired byproducts. On the other hand, palladium oxide produced propylene epoxide with fewer side products but at a slower rate. Combining the two catalysts, however, proved to be the solution, significantly improving the efficiency and rate of propylene epoxidation.
The resulting catalyst enhanced the rate of propylene oxide production by tenfold compared to previous methods, with a 13% increase in efficiency. Future research will focus on transitioning the catalyst from laboratory setups to industrial applications, analyzing its durability, performance at larger scales, and developing a process for extracting propylene epoxide from the system during production.
This article is republished from PhysORG under a Creative Commons license. Read the original article.
Do not forget to share your opinion with us to provide you with the best posts !
0 Comments